Porsche 919 Hybrid EVO (Farewell Tribute)
Background
At the end of 2017 Porsche decided to call themselves out of the FIA WEC (World Endurance Championship) from the LMP1 category, after having come back in 2014 and having won in 2015, 2016 and 2017.
The car was the 919 Hybrid , and at the end of 2017 it was developed to the 919 Hybrid EVO with the intention to destroy Stephan Bellof’s record, lasting since May 1983, at the Nürburgring track.
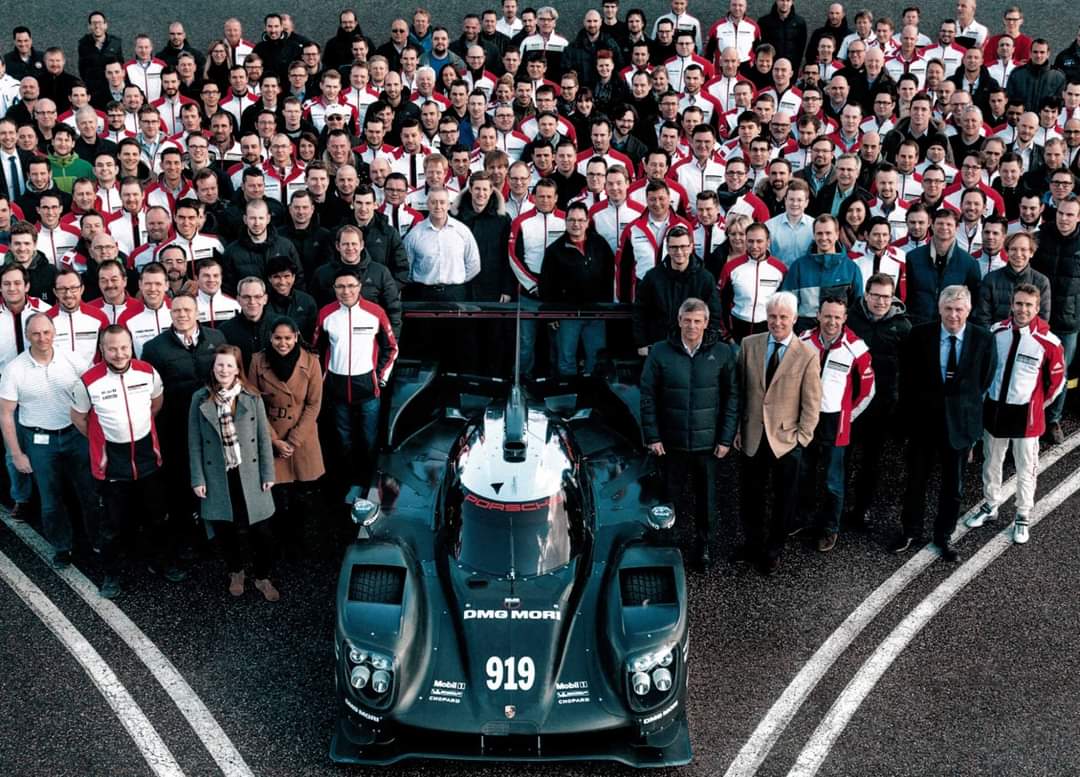
The Challenge
All the FIA regulations could be ignored, because the 919 Hybrid EVO would have not competed: both the thermal and the electric engines were tuned up, aero devices were used to increase the ground effect and DRS (Drag Reduction Systems) were put in place on both the front and the rear wings.
CG CAE was chosen as a partner to support the design team with simulations on the DRS, because of our wide experience in Motorsport and because we had already contributed to the victories in 2015, 2016 and 2017 Championships, supporting the design team with our simulation services.
The Rear DRS was based on the “standard” Formula One concept, with the flap being rotated by an actuator (Figure 1).
The DRS concept for the Front Wing (Figure 2) was completely new and quite ambitious: by not having a Flap, it was thought to reduce the drag by “pushing down” the trailing edge, again with actuators, in this case placed into the nose.

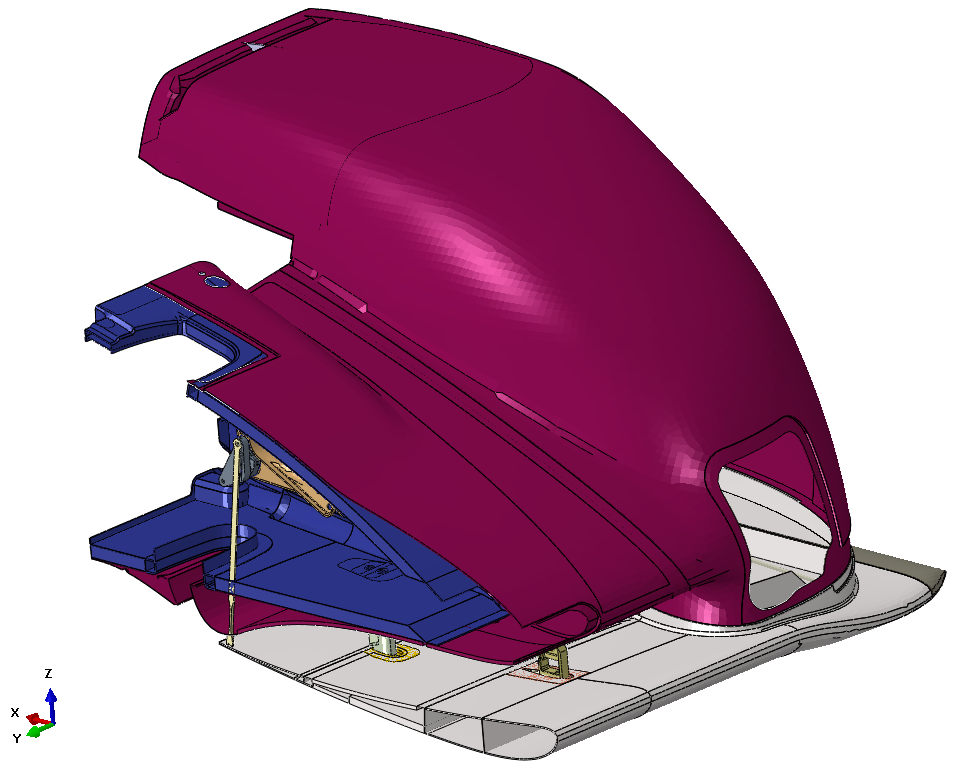
The FE Model
The real challenge has been to create a “continuous” hinge, by making, in the designated area, the carbon fibre structure flexible but strong at the same time. And here is were we have put in place our experience in dealing with hyperelastic materials and our knowledge in modelling their behaviour.
Nonetheless using embedded rubber layers into the laminate was not enough to keep the shear deformation within acceptable limits (from the aerodynamic point of view) and we therefore included very thin titanium plates. The challenge has been to find the right thickness and length of these sheets to get the best compromise between strength and flexibility: this was achieved only through simulations and a final test for confirmation.
The FE models have also been used to extract the forces required to activate the DRS, so to help in choosing the right actuators.
Some results
Figure 3 reports the displacement contour, showing that the trailing edge is clearly moving by a quite big amount compared to the rest of the wing.
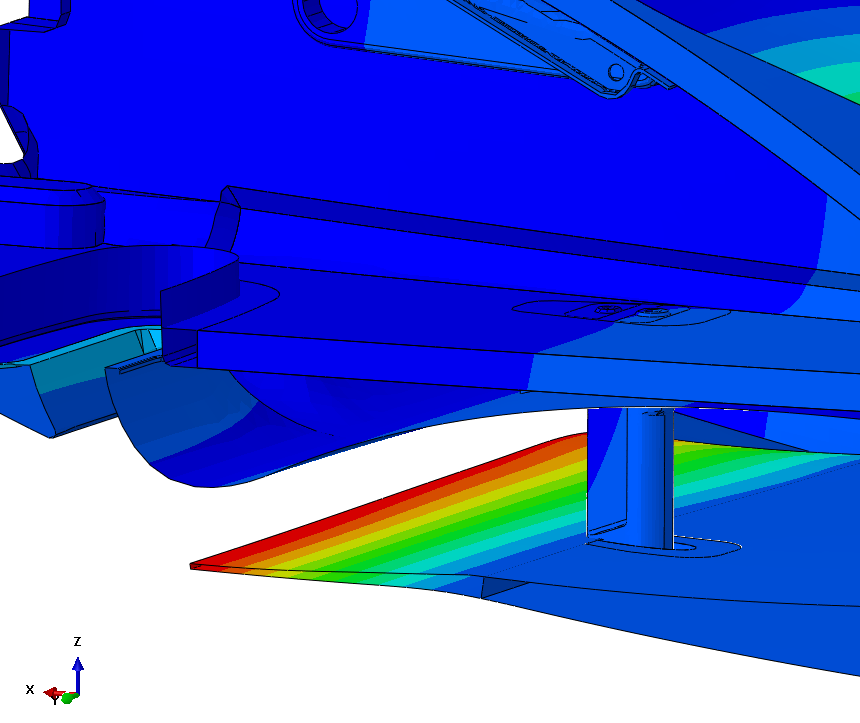
To better show this, an animation is provided here besides.
The deformed shape of the whole assembly was then given back to the CFD guys to allow them to perform some analyses on the actual reduction of the drag.
The Rear Wing was less interesting; the only challenge was to increase the stiffness of the assembly because, due to the mass of the DRS actuator, the first frequencies, especially the lateral ones, dropped below the design limits.
Conclusions
All the activities were carried out in a very short time frame and the 29th of June 2018 Timo Bernhard stopped the chrono at 5 minutes 19.546 seconds, breaking Bellof’s record by almost 52 seconds.