The “Superelement” Technique
At the times when low computational power and low memory capacity were available, the Superelement technique (more precisely defined as “substructuring“) was used to solve models with a high number of DOFs, while still staying within the limits imposed by the hardware. The method consists in dividing the complete structure to be analysed into substructures; for each of these blocks a finite element model is created, whose nodes lay on the separation lines (or surfaces) coincident with those of the adjacent substructure; for each block a “reduced stiffness matrix” is then determined at the interface nodes, which represents the elastic behavior of the related substructure at the points where it is calculated.
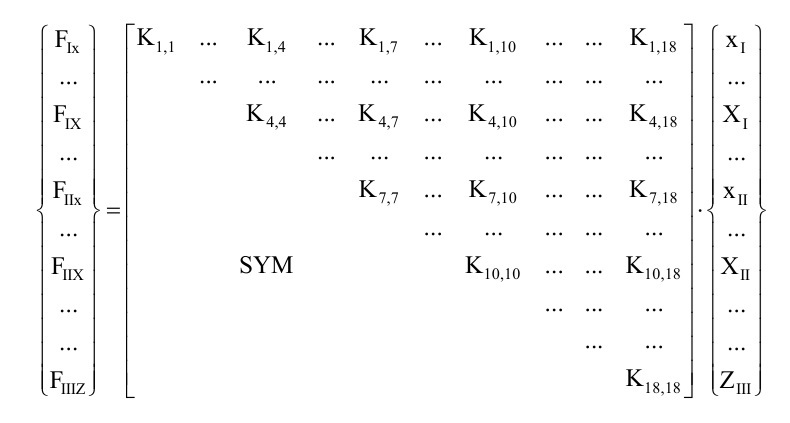
Nowadays, as mentioned above, thanks to the increasing availability of more and more powerful and cheap computers, this problem is much less felt, since it is possible to easily solve even structures with a few million degrees of freedom.
However the superelement technique can be profitably used, for example, when two different companies (perhaps using two different calculation codes) are analyzing two parts of the same structure which are interfaced: to verify separately and correctly the two substructures it is sufficient to exchange the respective stiffness matrices reduced to the interface points.
We observe that substructuring is somehow different from submodeling, discussed earlier in the News section, even if both of them allow to solve big structures with reduced computing resources.
Detailed information and a way to “manually” extract the reduced stiffness matrix of a structure (Superelement) can be found at Chapter 7 of the book “Computational Structural Engineering“.